What if the trash in your bin could effectively be converted into fuel for your next commercial flight, clean-burning heat that can power industrial processes, or valuable industrial materials? All while reducing the emission of greenhouse gases?
Thanks in part to CPM technologies and solutions, this is already happening at waste-to-energy plants around the globe, and will likely be an important piece of how we manage waste in the years and decades to come on a much larger scale.
The Waste Challenge
As a planet, we produce a lot of waste. In 2018, the World Bank estimated that we produce over two billion tons of municipal solid waste (MSW) every year, and they expect that number to grow to 3.4 billion tons by 2050.
Effectively dealing with, reducing, recycling, and reusing this waste is critical for the long-term health of our planet. At CPM, we offer a whole host of solutions that attack this challenge in a variety of ways. Our customers use CPM equipment and solutions to convert used tennis balls into playground bedding, turn broken shipping pallets and plastic bags into long-lasting building materials, perform bottle-to-bottle plastic recycling, and much more.
But, one of the most exciting applications for CPM solutions in waste management is waste to fuel.
Waste-to-Fuel Opportunities & Benefits
Broadly, “waste to fuel” refers to a range of technologies and processes that convert waste materials into usable fuels.
A wide range of waste products — from household garbage to industrial by-products, agricultural leftovers, and more — can be transformed into usable fuels through techniques that might include anaerobic digestion, biogas digestion, pyrolysis, gasification, and more.
The environmental benefits of waste to fuel come from two sources: 1) reducing greenhouse gas emissions from methane at landfills; and 2) creating green energy sources that can replace fossil fuels.
The potential benefits could be massive. Some estimates show that waste to fuel could produce CO2 reductions/sequestration of more than six gigatons between 2020 and 2050.
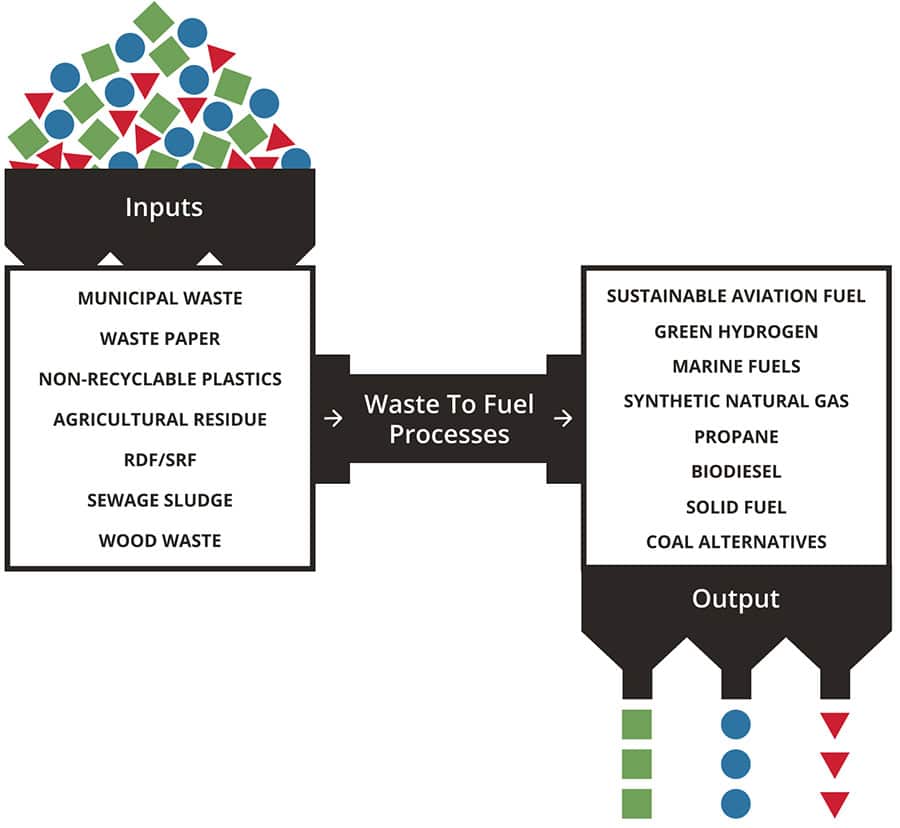
From Waste to Sustainable Aviation Fuel
One of the most exciting applications for waste-to-fuel operations is the production of sustainable aviation fuel (SAF). Both the EU and United States have ambitious goals for SAF requirements.
In the EU, 2% of jet fuel must be sustainable by 2025, 6% by 2030, 20% by 2035, and 70% by 2050. In the United States, several state and federal policies support the creation of SAF through tax credits and funding opportunities. The White House recently issued a “grand challenge” with the goals of 1) producing three billion gallons of SAF by 2030 and 2) enough SAF to meet 100% of commercial demand by 2050.
The EPA estimates that in the United States alone, one billion dry tons of biomass can be collected sustainably each year, which can be used to produce 50–60 billion gallons of low-carbon biofuel.
In the EU, the European Union Aviation Safety Agency (EASA) estimates that 2.3 million tons of SAF will be required by 2030. With a current estimated capacity of 0.24 million tons, it’s expected that the industry will see rapid growth during this decade.
CPM’s Waste-to-Fuel Solutions
CPM offers a variety of solutions for the waste to fuel industry including:
- Intelligent systems that automate and streamline waste material processing operations.
- Custom process engineering and equipment for end-to-end operations that turn agricultural waste into biofuels.
- Machinery for particle size reduction, sorting, drying and pelletizing – all of which are key processes in waste to fuel facilities.
“Waste is bulky and hard to handle,” explains Jorn van de Burgwal, Territory Sales Manager for CPM Industrial Solutions. “Turning it into pellets or briquettes is a key transformation that makes it suitable for many waste-to-fuel processes.”
CPM’s 7900 series pellet mills are an extremely popular option for waste-to-fuel pelleting applications. With over 2,000 installed globally, they’ve been proven to be robust, reliable, flexible, and highly efficient.
One single CPM partner has 10 CPM pellet mills installed at two waste-to-fuel plants where they process waste into more than 350,000 tons of pellets annually. A study performed by Ingenia in the Netherlands found that 1.6 tons of CO2 can be saved by every ton of fossil fuel substituted with waste fuel. According to that calculation, that single CPM partner plant is reducing 320,000 tons of CO2 emissions every year.
For small-scale municipal waste transformation facilities, briquetting represents the suitable solution, as it effectively transforms waste into high-calorific value fuels. CPM’s BRIK Series mechanical briquetting machines embody efficient and reliable technology for densifying various waste streams.
From Waste to Pellets
Before pelletizing or briquetting, mixed waste products go through a series of processes designed to separate, refine, and make the final product more suitable for the waste-to-fuel conversion process.
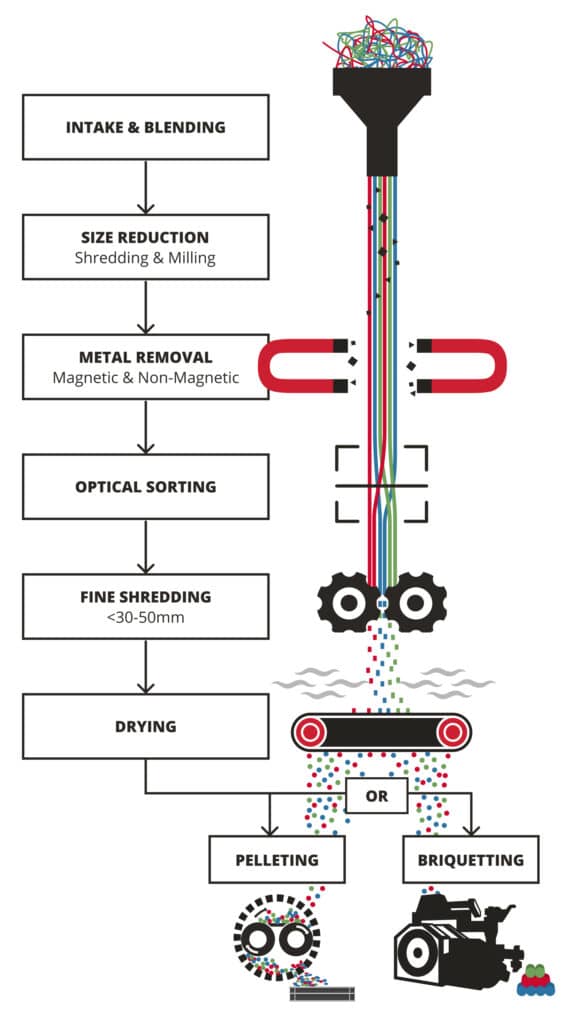
Partnerships for a Better World
If you’re looking for a partner to deliver reliable, proven waste-to-fuel or waste-to-energy processes, CPM would be happy to help.
“In the end,” says van de Burgwal, “utilizing waste for fuel is like mining valuable materials from the ground.” Only, in a more sustainable way that helps us to build a better and cleaner world.
Waste to Fuel Glossary
Looking to get up to speed on the latest in waste to fuel? Here are a few terms that might be helpful to understand.
Gasification – A process that converts organic or waste materials into syngas — a mixture of hydrogen, carbon monoxide, and carbon dioxide — by heating the materials at high temperatures in a low-oxygen environment. It is used in waste-to-fuel applications to transform municipal solid waste and other types of waste into a usable form of energy, reducing landfill use and producing clean, renewable fuel.
Fischer-Tropsch (FT) Process – A chemical reaction that converts a mixture of carbon monoxide and hydrogen, often derived from gasified waste materials, into liquid hydrocarbons. It can be used to convert waste into synthetic fuels like diesel or jet fuel.
Municipal Solid Waste (MSW) – Household garbage, yard waste, and commercial and industrial refuse. It encompasses a wide range of materials requiring management for disposal or recycling.
Pyrolysis – A thermal decomposition process that breaks down organic materials in waste at high temperatures in the absence of oxygen. It converts solid waste into a mix of gas, liquid bio-oil, and solid char, which can be used as renewable energy sources or chemical feedstocks.
Refuse-Derived Fuel (RDF) – A fuel produced from various types of waste, including non-recyclable plastics, paper, and other organic materials. It is created by processing and treating municipal solid waste to remove inserts and increase its energy content, making it suitable for use in energy generation.
Solid Recovered Fuel (SRF) – A high-quality fuel produced from non-hazardous waste materials. In the context of waste to fuel, SRF is processed and treated waste that has been sorted and refined to have a high calorific value, making it suitable for use in energy production.
Sustainable Aviation Fuel (SAF) – An eco-friendly fuel for aircraft, made from sustainable sources like waste products and agricultural residues. It reduces aviation’s carbon footprint by emitting up to 80% less carbon dioxide compared to conventional jet fuel, supporting the industry’s sustainability goals.
Waste to SAF (WtS) – A process that transforms waste materials, such as municipal solid waste or biomass, into sustainable aviation fuel.
Methane Digester – A system that breaks down organic material in a controlled environment to produce biogas, primarily composed of methane, which can then be used as a renewable energy source.
Biogas Digester – A device or facility that processes organic waste materials to produce biogas, a mixture of methane and carbon dioxide, which can be used as a source of renewable energy.
Biogas Generator – A system that converts biogas, produced from organic waste through digestion, into electricity or heat for practical use.